9 common problems and solutions in DTF printing
DTF Printing is the most popular printing process in the past two years. Our heat transfer white ink is highly recognized by the majority of printing customers for its advantages of good whiteness, good fluency and high fastness. As a new printing process, it is inevitable that some customers will encounter To all kinds of problems, in order to let everyone avoid detours when using, now the technical engineers of VISION DTF printing factory will share with you the common problems and solutions at this stage by technical test.
1.Whitening:Â It means that when printing some colors, especially color blocks, there will be unevenness.
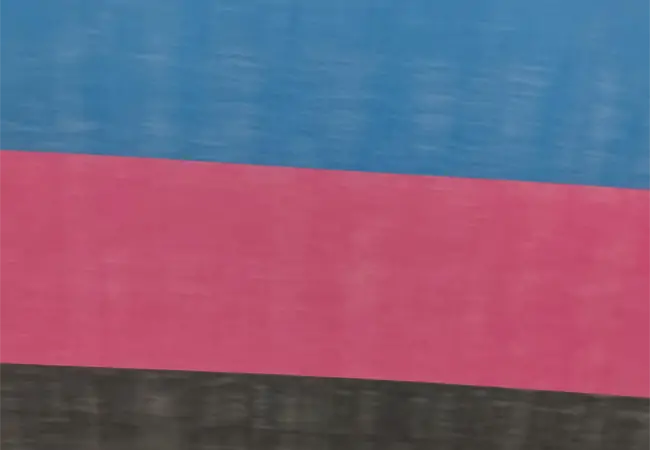
Whitening
Solution:
(1)When encountering such patterns, the printing accuracy and PASS number can be improved.
(2)The printing film can be replaced. According to experience, some films have poor ink absorption, but the color brightness and color uniformity are better.
2.Ink flow: It means that the film cannot absorb a large amount of ink when printing, and the ink cannot be fixed on the film. It will be more obvious in winter.
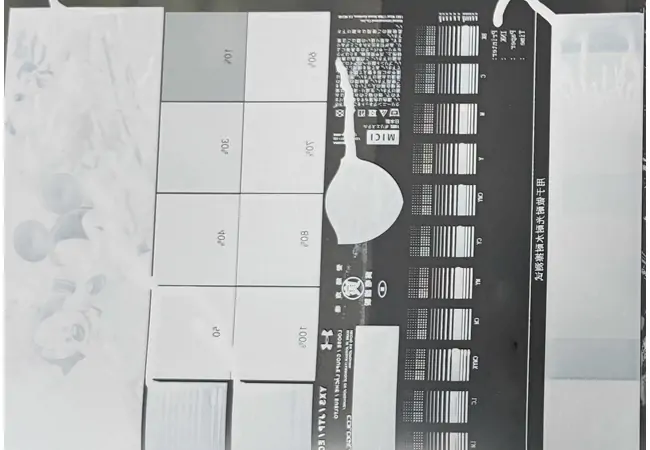
Ink flow
Solution:
(1)The platform heating of the printer is turned on.
(2)You can make an ICC with less ink.
(3)Check if the film is damp and replace the printing film.
3.The color is not bright:Â It means that the color difference of the pattern transferred to the fabric is poor and not bright enough.
Causes and Solutions:
In this case, it may be that the color rendering of the transfer film is not good. The above picture shows the effect of different film transfer. Another reason may be that the printing accuracy is not enough. Therefore, the solution can be to replace the film or improve the printing accuracy.
4. Poor release:Â It means that the film is difficult to tear after transfer, or some patterns remain on the film.
Causes and Solutions:
This is generally the coating of the film is not good enough, which requires replacing the printing film.
5.Oil return, oil stains on the screen, poor fastness:Â It means that the film with the melted powder is placed on the next day, and there are many oil stains on the surface. Or the pattern after transfer has oil stains and indentations on the surface. There are even some patterns. Just after the transfer came out, the surface became oily after standing for 1 hour.
There are several reasons for this problem: the temperature is too low when melting the powder, the melting point of the glue powder is too low, the amount of ink is too large, the time for melting the powder is not enough, etc. If the melting point of the powder is too low, when the melting powder is heated, the glue The powder will quickly melt and seal the water and solvent in the ink under the hot melt adhesive, resulting in problems such as oil return and poor fastness.
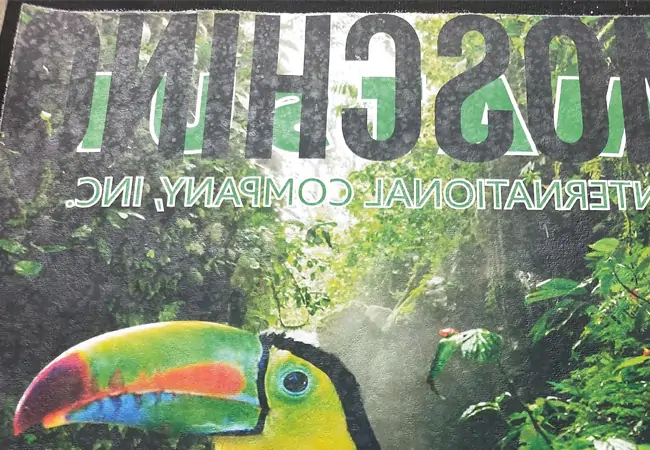
Oil return
Solution:
(1)The printer is heated and turned on, and pre-drying is turned on before dusting, so that the water in the ink and the solvent will evaporate first. But this may have a disadvantage, the amount of sticky powder in the picture will be relatively reduced, and some small places may be The fastness is affected by the lack of powder.
(2)Use powder with a slightly higher melting point and increase the melting temperature, increase the tunnel length of the powder shaker, or put the picture of the melted powder into the oven or tunnel to bake again.
6. Shrinkage:Â It means that after the powder is melted, there are small black dots on the picture. When the picture is facing the light, you can see that the black dots are small holes one by one. The reason for this situation is generally that the picture does not The powder is pre-dried, and the powder with low melting point is used. When the powder with low melting point is melted at a higher temperature, the violent melting of the powder destroys the image below.
Solution:
(1)Pre-dry before powdering.
(2)Use powder with a slightly higher melting point.
7. Cut off the ink:Â There are broken holes during white ink printing. There are two cases here, one is scattered random broken holes, and the other is that the entire channel does not appear. The reason: one is that the ink flow is not enough. Another reason is that the white ink will adhere to the wall of the ink tank and the stirring rod during use. With the continuous printing, the liquid level becomes lower and adheres to the wall of the ink tank, and the white ink on the stirring rod will agglomerate. Again When adding ink, due to the rotation of the stirring rod, the agglomerated part falls off, causing ink pollution. After the fine particles enter the print head, they will slowly block the filter screen of the print head, resulting in no ink from the entire channel of the print head. The other is the circulating ink path Impurities will also be produced. Too much impurities will continue to affect the fluency of the ink.
Solution:
Clean the ink tank and the ink path. If the entire channel of the print head does not go out, you can first check whether the return pump is turned too small. In addition, you can also try to clean the nozzle by reverse extraction (see the nozzle cleaning video in the accessories), and add filters to the ink outlet and ink inlet tube of the white ink tank. It is recommended to clean the white ink tank once a week.
8. Stick to the powder: It means that some powder sticks to the edge of the picture after transfer. It affects the effect of the picture, and the dense small characters are most likely to stick to the powder.
Solution:
(1)After tearing the film, press it with a pressing machine for 1-2 seconds.
(2)Use a powder with a larger particle size.
Adjust the speed and strength of the shaker.
9. Other aspects?
(1)From personal experience, at this stage, in the film, the color vividness, ink absorption, whitening, and release.
It is difficult for all 4 indicators to be excellent. It is easier to use if they can be balanced.
(2)When the white ink is stored, the test customer should turn it over every 2 days. Shake it more when using it. The dealer may have a longer inventory time, and it is not suitable for frequent turning over because of the large amount. It is recommended that customers prepare an ultrasonic wave, Before shipment, shake it with ultrasonic wave for 3 minutes, then shake it again before shipment.
(3)After turning on the machine every day, print the nozzle test strip before turning off the machine. If there is a broken needle, it needs to be cleaned.
If there is a broken needle, it should be cleaned in time. The machine does not need to be cleaned for more than 3 days.
Inject the moisturizing liquid, and then put the nozzle back in place. If it is not used for more than 7 days, you need to put all the nozzles.
Clean and inject moisturizing liquid. The ink tank and ink tube of white ink should also be cleaned. If it is not used for more than 15 days, all ink tanks, ink tubes and nozzles should be cleaned, and the nozzles should be filled with moisturizing liquid.
(4)It is recommended to melt the powder at a temperature of 145-150 degrees for 150 seconds, and press at a temperature of 150-165 degrees for 10-15 seconds.
(5)It is recommended that the temperature of the working environment be controlled between 22-28 degrees, and the humidity should be controlled between 55%-65%.
The above suggestions are only applicable at this stage. With the update of technology, the process will be continuously optimized. If you have any other questions, please contact our company.