Best Heat Settings for PU Heat Transfer Vinyl
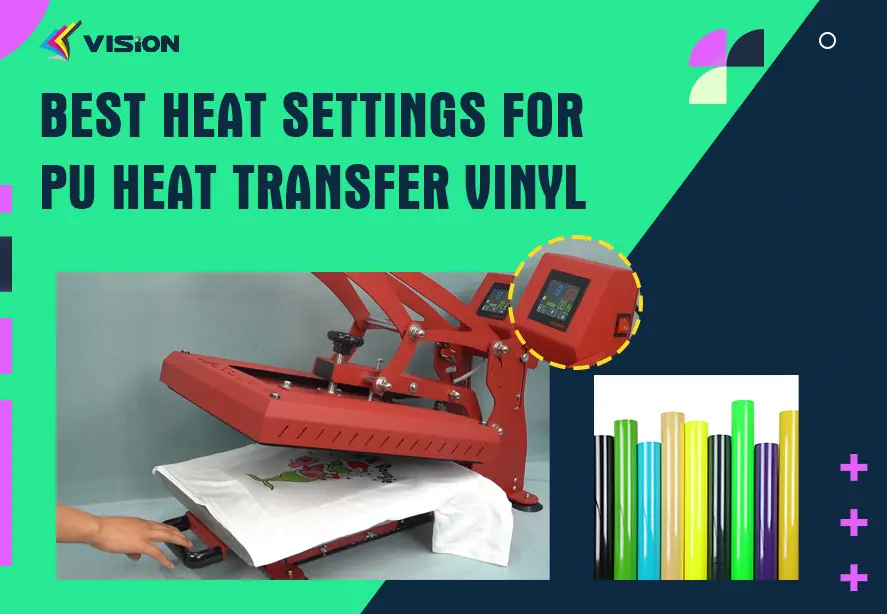
Heat transfer vinyl has become a popular choice for customizing clothing, accessories, and other fabric items. Polyurethane (PU) heat transfer vinyl, in particular, is known for its durability and versatility. However, achieving the perfect application requires understanding the best heat settings for this material. In this article, we’ll explore the optimal temperature, pressure, and time settings for PU heat transfer vinyl to help you achieve professional-looking results.
Understanding PU Heat Transfer Vinyl
Before diving into the heat settings, it’s essential to understand what PU heat transfer vinyl is and why it’s widely used:
- PU HTV is a thin, flexible material made of polyurethane
- It’s known for its soft feel and durability
- PU HTV is ideal for a wide range of fabrics, including cotton, polyester, and blends
Optimal Heat Settings for PU Heat Transfer Vinyl
Temperature
The ideal temperature for applying PU heat transfer vinyl typically ranges from 300°F to 320°F (150°C to 160°C). However, it’s crucial to note that this can vary slightly depending on the specific brand and type of PU HTV you’re using. Always check the manufacturer’s recommendations for the most accurate temperature settings.
Pressure
Pressure is a critical factor in ensuring proper adhesion of the PU HTV to the fabric. For most PU heat transfer vinyl applications, medium to firm pressure is recommended. This translates to approximately 40-50 PSI (pounds per square inch) on a heat press machine.
Time
The duration of heat application is equally important. For PU heat transfer vinyl, the typical pressing time ranges from 10 to 15 seconds. However, this can vary based on the thickness of the vinyl and the fabric you’re applying it to.
Step-by-Step Application Process
Preheat your heat press to the recommended temperature (300°F to 320°F).
Place your garment on the heat press, ensuring it’s smooth and wrinkle-free.
Position your PU HTV design on the garment, with the carrier sheet facing up.
Cover the design with a Teflon sheet or parchment paper to protect it and the heat press.
Close the heat press, applying medium to firm pressure for 10-15 seconds.
Open the press and allow the design to cool for a few seconds.
Peel off the carrier sheet. If it’s a cold peel vinyl, wait until it’s completely cool before removing.
Tips for Success
Always do a test press on a scrap piece of fabric before applying to your final product.
Ensure your heat press is properly calibrated for accurate temperature and pressure readings.
If you’re working with layered designs, press each layer separately, reducing the time for subsequent layers to prevent over-curing.
For fabrics sensitive to high heat, consider using a lower temperature and increasing the pressing time slightly.
Troubleshooting Common Issues
Vinyl Not Adhering Properly
- If you find that the vinyl isn’t sticking to the fabric, try:
- Increasing the temperature slightly
- Applying more pressure
- Extending the pressing time by a few seconds
Vinyl Melting or Discoloring
If the vinyl appears to be melting or changing color, you may need to:
- Reduce the temperature
- Decrease the pressing time
- Ensure you’re using a protective sheet between the vinyl and the heat press
Mastering the best heat settings for PU heat transfer vinyl is key to achieving professional-quality results in your projects. By understanding the optimal temperature, pressure, and time settings, you’ll be well-equipped to create durable and attractive designs on a variety of fabrics. Remember to always test your settings and follow the manufacturer’s recommendations for the specific PU HTV you’re using. With practice and attention to detail, you’ll soon be creating stunning custom designs with ease.
Related:
What Makes PU Heat Transfer Vinyl Unique?
How To Layer PU Heat Transfer Vinyl?